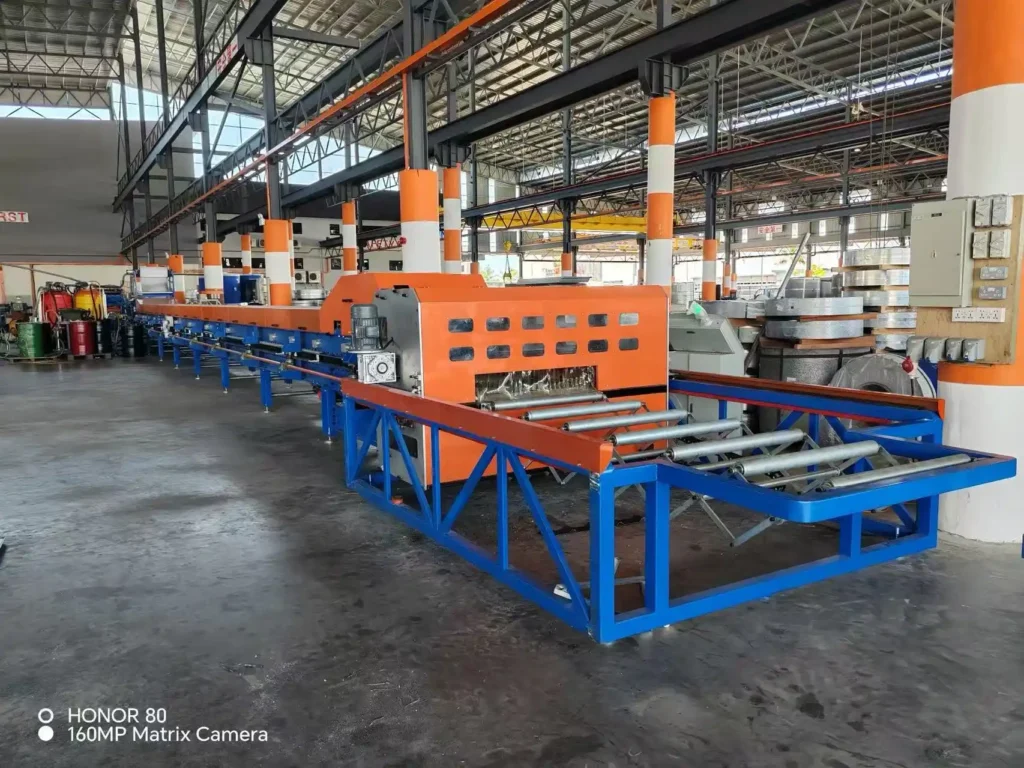
In the construction and manufacturing industries, the demand for lightweight, durable, and energy-efficient materials has led への the widespread use of sandwich panels. These panels, known for their excellent thermal insulation and structural strength, are produced through specialized machinery known as sandwich panel machines. This ブログ explores the key components, workflow, benefits, and trends associated with sandwich panel machines. Whether you’re a manufacturer looking への upgrade your production line or someone exploring this technology for the first time, understanding these machines can significantly improve your production efficiency and 製品 quality.
What is a Sandwich Panel?
A sandwich panel is a type of composite building material consisting of two layers of high-strength metal sheets (usually steel or aluminum) bonded への an insulating core material in the middle. This “sandwich” structure combines lightweight design, excellent strength, thermal insulation, and durability.
It offers structural efficiency—such as superior tensile and compressive strength from the dual metal layers, while the lightweight core reduces overall weight without sacrificing load-bearing capacity—making it suitable for wide-span roofs, wall cladding, and modular buildings.
Sandwich panels also provide outstanding thermal insulation (the core effectively blocks heat transfer, reducing energy consumption), enhanced fire resistance and safety (some core materials like rock wool are fire-resistant and improve the building’s fire rating), and ease of installation (modular design enables quick and efficient assembly).
サンドイッチ・パネル・マシンとは?
A sandwich panel machine is a specialized mechanical system designed for the automated production of sandwich panels, which are composite building materials composed of two metal face sheets bonded to a core insulation layer. This machine integrates advanced manufacturing processes, including continuous roll-forming, laminating (compounding the core material with the metal sheets), and precision cutting, enabling high-efficiency, large-scale production. Among the various types, the PU Sandwich Panel Machine is a prominent example, focusing on the production of panels with a polyurethane (PU) foam core. This machine ensures consistent quality, rapid output, and adaptability to different panel specifications, meeting the demands of modern construction projects for lightweight, energy-efficient, and durable building materials.
Components and ワークフロー
Components
- フィーディング and Discharge System
Responsible for automatically feeding metal panels and discharging finished products, reducing manual intervention and improving production efficiency. - Roll 成形 System
Through multiple sets of continuous rollers, the metal panels are gradually pressed into the desired shapes (such as corrugated or flat), ensuring structural strength and dimensional accuracy. - Glue Coating System (for PU and other core materials)
Uniformly applies polyurethane (PU) or other adhesives への the metal panel surface への ensure strong bonding between the core material and the panel. - Insulation Core Material フィーディング Device
Automatically feeds core materials such as polyurethane foam or rock wool への the composite station, supporting flexible adjustments of core thickness and density. - Composite Pressing Device
Uses hydraulic or mechanical pressure への tightly bond the formed metal panel with the core material, creating a high-strength composite structure. - Automatic Cutting System
Precisely cuts the composite panels according への preset dimensions (e.g., length, angle) への meet diverse engineering needs. - Control System (PLC Touch Automation)
Integrates PLC (Programmable Logic Controller) and touch screen for full-process automation control, parameter adjustment, and fault diagnosis.
Production ワークフロー
- フィーディング of Metal Panels
について feeding and discharge system transports the metal panels (such as color-coated steel plates or aluminum plates) への the roll forming station. - 成形
について roll forming system continuously presses the metal panels into the desired wave or flat shape. - Core Material Filling/Composite
について insulation core material feeding device fills the formed panels with core materials (e.g., PU foam), while the glue coating system simultaneously applies adhesive. - Pressing
について composite pressing device applies pressure への ensure the core material is tightly bonded への the panel, eliminating any gaps. - Curing
Core materials such as PU undergo chemical curing (e.g., foam reaction) under pressure への form a stable composite structure. - Cutting and Shaping
について automatic cutting system cuts the panels への the required length or shape according への the order, completing the 製品 discharge.
Note:
- Modular Design:
Each system can be independently debugged or operated in conjunction, adapting への the production needs of different types of sandwich panels. - Energy-efficient and High-performance:
について PLC control system optimizes process parameters, reducing material waste and energy consumption, improving capacity, and ensuring consistent 製品 quality.
メリット of Using a Sandwich Panel 機械
High-efficiency Production – Time- and Labor-saving
A sandwich panel machine enables a fully automated, continuous production process—from metal panel forming への core material compounding and cutting—all seamlessly integrated. Compared への traditional manual or semi-automated methods, this equipment significantly shortens production cycles, operates efficiently around the clock, boosts output, and reduces both labor intensity and time costs.
High-precision Manufacturing – Stable and Reliable Quality
With precision roll forming and automated control systems, the machine ensures accurate control over panel dimensions, uniform thickness, and flat surfaces. This guarantees consistent physical properties and appearance quality of each sandwich panel, making it ideal for industries with strict precision requirements such as construction, cold chain logistics, and cleanroom engineering.
Reduced Labor Costs – Improved Economic メリット
について highly automated production process drastically reduces reliance on manual labor. Only a few operators are needed for equipment monitoring and maintenance, cutting labor costs and minimizing quality fluctuations or delays caused by human error—ultimately improving overall operational efficiency and profitability.
Strong Versatility – Meeting Diverse Needs
について machine allows for quick mold changes and process parameter adjustments, enabling flexible production of sandwich panels with various thicknesses (e.g., 50–200 mm), カスタマイズ lengths, and different core materials (e.g., polyurethane, rock wool, EPS). This adaptability suits a wide range of applications such as industrial buildings, cold storage, temporary structures, and cleanrooms.
Support for Custom Production – Quick Market Response
Users can customize sandwich panels for special specifications (such as irregular cross-sections or built-in reinforcements) or functionalities (such as fire resistance or sound insulation) by changing molds or adjusting settings. This flexibility helps manufacturers respond quickly への market demands and enhances their competitive edge.
Practical Tips for Buying a Sandwich Panel 機械
- Define Your Needs Clearly – Specify 製品 Requirements
Panel Type and Dimensions: Identify the specific types of sandwich panels needed (e.g., corrugated, flat, or custom-shaped panels) and the common size range (length, width, thickness) based on your target market or project demands. This ensures the equipment capacity aligns with actual production needs.
Core Material Compatibility: Confirm the types of core materials への be used (e.g., polyurethane [PU], rock wool, expanded polystyrene [EPS]) and ensure the equipment supports corresponding bonding processes. It’s also wise への leave room for future upgrades への accommodate new materials. - Evaluate Equipment Capacity and Automation Level
Capacity Matching: Choose equipment with a production capacity (e.g., hourly output, max cutting length) that fits your production scale and order volume への avoid overcapacity or bottlenecks.
Automation Level: Prioritize fully automated production lines (e.g., auto-feeding, glue application, compounding, cutting) への reduce manual intervention and improve efficiency and consistency. If budget is limited, consider phased automation upgrades. - Manufacturer Strength and After-sales Support – SKD is a Smart Choice
Technical Capability and Reputation: Opt for manufacturers with strong R&D capabilities and rich industry experience. You can verify equipment stability and process maturity by checking case studies and customer reviews.
After-sales Service: Choose manufacturers that offer SKD (worry-free after-sales) services, including equipment installation, operator training, regular maintenance, 24/7 technical support, and fast spare parts supply への ensure long-term stable operation. - Balance Budget and Cost-effectiveness – Avoid Blindly Chasing Low Prices
Cost Analysis: Consider the total cost of ownership, including purchase price, energy consumption, maintenance costs, labor input, and the product’s added value. Calculate the long-term return on investment (ROI).
Prioritize Value: Within your budget, choose machines that are technologically mature, energy-efficient, and reliable, instead of going for the cheapest option. Poor-quality equipment may lead への production interruptions and higher operating costs. - Pay Attention への Optional Upgrades and Expansion Capabilities
Modular Design: Select equipment that supports modular upgrades (e.g., future addition of automated packaging lines or smart warehousing systems) への scale production or functionality flexibly as your business grows.
Smart Expansion: Prioritize machines compatible with Industry 4.0 technologies (e.g., data acquisition, remote monitoring, AI-powered fault alerts) への future-proof your investment and stay competitive in the market.
結論
As the construction industry shifts toward greener and smarter practices, sandwich panel production equipment is emerging as a key driver of industrial upgrading in modern construction. Known as a “versatile performer” in the field of composite building materials, sandwich panels are lightweight, high-strength, fire-resistant, and offer excellent thermal insulation and weather durability. These advantages have led への their widespread adoption across various sectors, including industrial plants, cold chain logistics, modular buildings, and cleanroom projects.
With the advancement of global green building policies and the increasing adoption of prefabricated construction, market demand for sandwich panels continues への surge. Their irreplaceable role is especially evident in emergency applications such as temporary buildings and post-disaster reconstruction.
At the same time, the ongoing evolution of intelligent and modular equipment is unleashing new technological advantages. Automated production and precise process control significantly reduce energy consumption and labor costs, while enhancing 製品 consistency and customization capabilities. This positions companies への capture high-end market opportunities, driven by a synergistic combination of policy support, growing demand, and technological empowerment—opening a vast industrial blue ocean for sandwich panel equipment.