With the rapid development of construction technology, the requirements of roofing systems are constantly upgrading. From traditional tile roofs to modern metal roofs, the construction industry has entered a new stage. In this process, “standing seam roofing” has gradually become the first choice for high-end construction projects with its unique design and excellent performance. This type of roof not only meets the basic requirements of waterproofing and wind resistance, but also has a modern and beautiful appearance. Behind all this, the Standing Seam forming machine is the hero behind these design concepts. It transforms ordinary metal sheets into strong, durable and modern roofing materials.
Standing Seam roofing: Defining a new standard for building roofs
The so-called Standing Seam roofing, as the name suggests, is to form a standing “gap” structure with the seams of metal sheets through special processing technology. This design not only makes the roof panel more solid, but also effectively prevents moisture penetration because the seams are higher than the roof surface. Unlike traditional roofing systems, standing seam roofs have stronger wind pressure resistance and tensile strength, especially in extreme weather conditions, and can remain stable, avoiding problems such as roof damage or water seepage.
Another major advantage of standing seam roofs is their simple and modern appearance. Because the joints are designed as high-standing gaps, the roof looks more layered and visually impactful, and this design has become part of today’s architectural aesthetics. In order to meet these high-standard roofing requirements, the Standing Seam forming machine came into being and became the core equipment for producing high-quality standing seam roof panels.
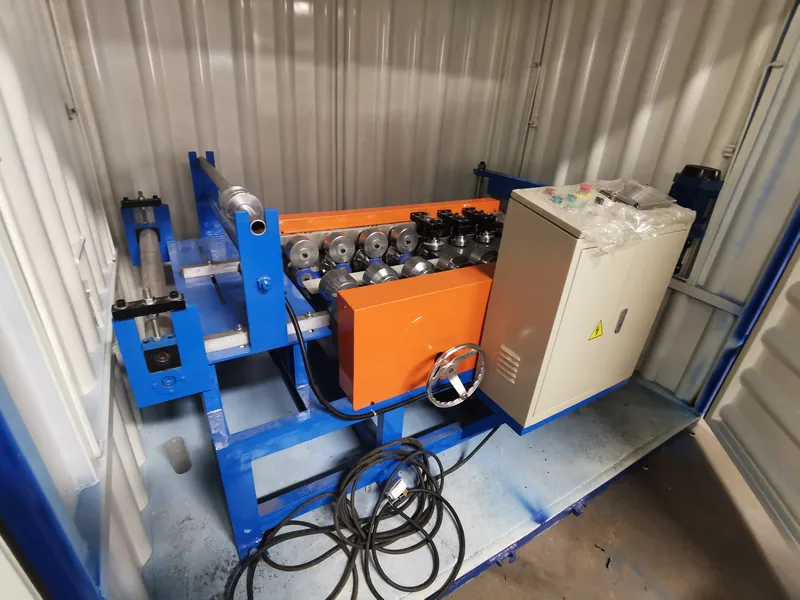
Standing Seam forming machine: efficient and precise production process
The Standing Seam forming machine transforms metal coils into roof panels that meet design standards through a series of precise mechanical processing. Behind the seemingly simple equipment, its working principle and precision process are full of wisdom. Its main work process includes: unwinding, forming, cutting, discharge and sorting. Each step is crucial to ensure the accuracy and quality of the roof panels.
Uncoiling and feeding: The forming process starts with the uncoiling of the metal coil. After the uncoiling machine, the feeding device feeds the metal sheet into the forming machine. This process ensures that the surface of the sheet is flat and wrinkle-free, and can smoothly enter the subsequent forming steps.
Forming roller: This is the core part of the Standing Seam forming machine. The metal sheet is gradually pressed into the shape of the seam through a series of high-precision roller groups. The precision design of each roller group can ensure that the angle, thickness and shape of the roof panel meet the design standards. The roller group system can control the forming path of the metal sheet to achieve the ultimate in accuracy and efficiency.
Cutting and shaping: After the forming is completed, the automatic cutting system of the forming machine accurately cuts the metal sheet according to the predetermined length to ensure that each roof panel meets the construction requirements and has the same size, avoiding installation difficulties caused by errors.
Discharge and sorting: Finally, the formed roof panels are neatly discharged through the automated discharge system, ready for subsequent transportation and installation. This process maximizes production efficiency, reduces manual intervention, and ensures the smoothness of the entire production line.
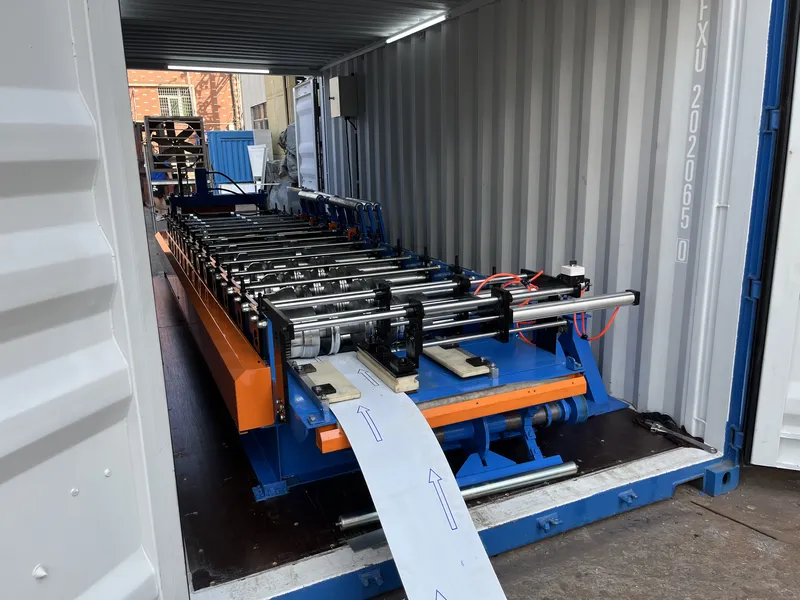
Advantages and application scenarios of Standing Seam forming machine
The Standing Seam forming machine is not just a machine, it represents the construction industry’s continuous pursuit of precision, efficiency and environmental protection. Its advantages include:
Efficient production: With a high degree of automation, the entire production line requires almost no human intervention. From unwinding to cutting, each link can be completed accurately and quickly, with extremely high production efficiency. Compared with traditional manual operation, the forming machine greatly saves time and cost.
High precision: Through the precise roller group design, the Standing Seam forming machine can ensure that the size and shape of each roof panel are consistent, avoiding errors caused by human operation, and ensuring that each roof panel can accurately match the actual installation requirements.
Extreme durability: The metal roof itself has strong durability, and the roof panels processed by the Standing Seam forming machine are not only wind-resistant and earthquake-resistant, but also can withstand the test of extreme climates, reducing maintenance and replacement frequency.
Modern appearance: Standing Seam roofs not only have excellent functionality, but also have a modern and simple appearance, which can add a sense of technology and art to the building, and are especially suitable for high-end construction projects.
Standing Seam forming machines have a wide range of applications. They are not only used in commercial buildings, industrial plants and storage buildings, but also in agricultural facilities, public buildings and other fields. Whether it is a region with a harsh climate or a construction project that pursues both beauty and functionality, the Standing Seam forming machine can provide high-quality roofing solutions.
Why choose Standing Seam forming machines?
With the increasing development of construction technology, a single roofing solution can no longer meet the needs of modern buildings. Standing seam roofs have become the first choice for more and more construction projects due to their excellent waterproofness, wind resistance, durability and beauty. As the core equipment of this roofing system, the Standing Seam forming machine is helping builders to produce roof panels that meet modern needs more efficiently and accurately.
The use of Standing Seam forming machines can not only improve production efficiency and reduce labor costs, but also ensure that the quality of each roof panel meets international standards, thereby providing builders and end users with more stable and high-quality roofing solutions. The popularity of this equipment marks an important step forward in the intelligentization and automation of the construction industry.
The Standing Seam forming machine is not only a key equipment for roof production, but also a booster to promote the construction industry to a higher standard. Through this efficient and precise machine, builders can produce better quality roof panels, which not only meet the needs of modern buildings for safety, durability and beauty, but also improve production efficiency and reduce production costs. As the construction industry continues to increase its requirements for roofing systems, the Standing Seam forming machine will continue to play an irreplaceable role and provide more solid and reliable roof protection for global construction projects. If you are looking for a roofing solution that emphasizes both functionality and beauty, the Standing Seam forming machine is undoubtedly your best choice.